Дата публикации: 20.03.2022
Калиев Ербол Батырханович
к.т.н., ассоц. профессор, Академия логистики и транспорта, г. Алматы, Казахстан
Жуманов Мерген Амирович
к.т.н., ассоц. профессор Казахский национальный университет имени Aль-Фараби,
г. Алматы, Казахстан
Абдувайс Сержан
магистрант, Академия логистики и транспорта, г. Алматы, Казахстан
Аннотация
Рассмотрены технические аспекты совершенствования подшипников скольжения в поршневых двигателях внутреннего сгорания при использовании различных материалов для вкладишей и шеек коленчатых валов. Выбор материала для изготовления подшипников скольжения для двигателей внутреннего сгорания является важным фактором повышения их надежности и увеличения их строка службы.
Ключевые слова: подшипники скольжения, термическая стойкость, теплопроводность, вкладыш, фрикционный контакт, маслянный клин.
В подшипнике скольжения поверхность втулки вала и опорной поверхности подшипника образует фрикционный контакт, в котором возникает, в зависимости от условий работы один из видов трения–жидкостное, граничное либо полусухое или даже сухое трение.
Из теории подшипников [2,3] следует, что сила трения и интенсивность изнашивание поверхности трения в большой степени зависит от взаимодействия материалов во фрикционном контакте трущихся деталей.
Одним из основных процессов, нарушающих работу подшипника, является схватывание материалов.
Схватывание происходит при любых температурах и не зависит от времени контакта поверхностей, но оно интенсифицируется при повышении температуры.
Поэтому интенсивный отвод тепла от локальных зон, в которых происходит граничное или полусухое трение с выделением тепла, является одним из основных требований для работы подшипников скольжения.
Принимая температуру плавления материала как предельную, при которой схватывание может развиваться лавинообразно, был сформулирован параметр термической стойкости подшипника и определены его численные значения. Параметр термической стойкости представляет собой произведение коэффициента теплопроводности на температуру плавления.
Для удобства сравнения материалов между собой была принята относительная величина параметра термической устойчивости. При этом относительная величина рассматривалась в двух вариантах, при принятии за исходную базу баббит, как классический материал подшипников скольжения, базу алюминиево-оловянный сплав, используемый в стандартных подшипниках скольжения для выполнения опорных поверхностей вкладышей. Рассматривая результаты такого сравнения, можно видеть, почему был применен алюминиево-оловянный сплав при изготовлении стандартных вкладышей. У него параметр термической устойчивости в девять раз превышает таковой для баббита.
Учитывая невысокую цену металлов для изготовления таких вкладышей, а также отработанную технологию массового их производства, заключающуюся в совместной прокатке фрикционного контакта (стальная подложка и алюминиевый сплав в качестве опорной поверхности вкладыша), можно понять, почему такие вкладыши нашли широкое применение в двигателестроении.
Из таблицы также следует, что алюминиево-оловянный сплав обладает далеко не предельными свойствами, обеспечивающими термическую устойчивость подшипников скольжения. Медь в чистом виде обладает показателем термической устойчивости в три раза более высокой, чем алюминиево-оловянный сплав и в 28 раз более высокой по сравнению с баббитом.
При этом все другие цветные металлы в чистом виде (алюминий, магний, кремний, свинец, олово), а также сплавы на основе меди– латунь и бронза не имеют преимуществ не только перед медью, но и перед алюминиево-оловянным сплавом, так как у них значение параметра термической устойчивости значительно меньше.
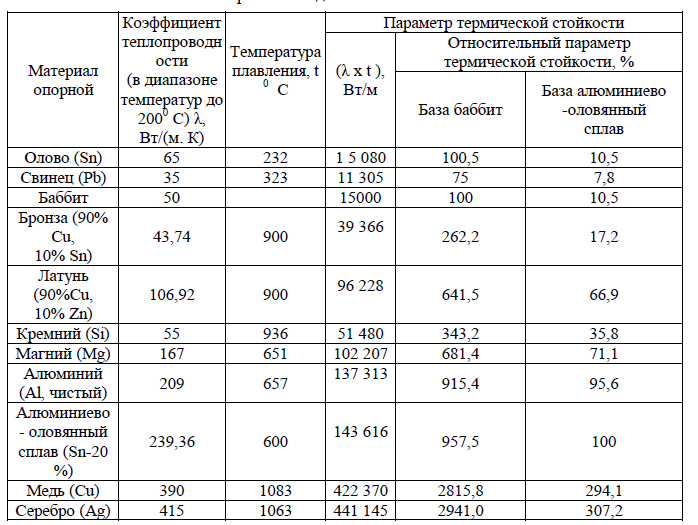
Даже такой металл, как серебро, обладающий в природе наиболее высокой теплопроводностью, имеет параметр термической стойкости только на 4% превышающий значение для меди, но, что естественно, по стоимости он несоизмеримо более дорогой.
Другие свойства меди, такие как твердость, пластичность, наличие пленки окисла по твердости мало отличающейся от твердости основного металла, технологичности обработки (возможность прокатки, штамповки), также показывают целесообразность использования меди для выполнения опорных поверхностей подшипников скольжения.
Этот результат позволяет сделать вывод, что подшипники с медными вкладышами позволяют существенно повысить качество подшипников скольжения.
С целью подтвержденияэтого вывода для подшипников скольжения кинематических механизмов ДВС было проведено экспериментальное определение интенсивности изнашивания подшипников на машине трения.
Методика эксперимента подбиралась таким образом, чтобы испытание проводились в близких к реальным условиям эксплуатации подшипника в механизме ДВС, но при этом в ускоренном режиме [4], для этого использовался корпус стандартного подшипника шатуна при диаметре шейки вала 50 мм и шириной 25 мм.
Радиальная нагрузка на подшипник задавалась равной 250 Н, что создавало на подшипнике удельную нагрузку 250 кг/см2, близкую по величине, возникающей в реальных условиях в ДВС.
Но нагрузка воздействовала во время опыта постоянно, и только на одну сторону подшипника.
По расчету режима работы подшипника под заданной нагрузкой в машине трения в течение 220 ч подшипник СА алюминиевым вкладышем, произошло одностороннее изнашивание, соответствующее работе подшипника в реальном двигателе при импульсной нагрузке за 1500 мото-часов.
Первая серия опытов на машине трения проводилась с установленными алюминиево-оловянными вкладышами. В этой серии опытов было подтверждено, что процесс изнашивания подшипника происходит по классической зависимости.
За время 8-10 ч происходит приработка фрикционного контакта, после чего наступает стабильный режим изнашивания с интенсивностью 0,0002 г/ч или в объемных единицах 0,000074 см3/ч.
После работы подшипника под нагрузкой в течение 230 ч интенсивность изнашивания резко возрастает, процесс переходит в режим ускоренного изнашивания.
Переход с с режима стабильной работы на режим ускоренного изнашивания произошел при потере массы вкладыша 0,08 г, при которой радиальный зазор в подшипнике достиг предельной допустимой величины
0,15 мм.
Отметим, что именно величина зазора в подшипнике определяет его ресурс, так как при увеличении зазора сверх допустимой техническими условиями величины, нарушается режим образования масляного клина, обеспечивающего жидкостное трение.
Другая серия опытов проводилась в тех же условиях, но с медными
вкладышами.
Обработка результатов опытов этой серии показала, что изнашивание происходит с интенсивностью 0,000135 г/ч, или в объемных единицах 0,000015 см3/ч, т.е. по объемным величинам, в 5,0 раза менее интенсивно, чем для алюминиевого вкладыша.
При этом режим интенсивного изнашивания не был достигнут.
Сравнительные данные работы подшипника с медными вкладышами и стандартными подшипниками с алюминиево-оловянной поверхностью скольжения проводилось по относительной величине зазора, принимая за 100% условия, которые создаются после приработки подшипника.
На рис. 2 приведены сравнительные изменения относительной и максимальной (в%) величин зазора в стандартном подшипнике и подшипнике с медными вкладышами.
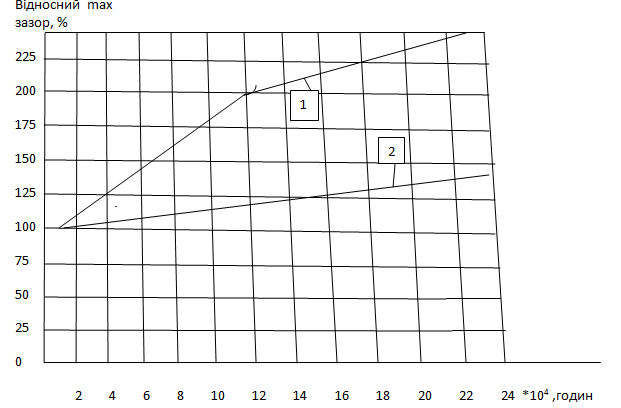
1 – стандартный подшипник с вкладышем с алюминиево-оловянной скользящей поверхностью; 2 – медный вкладыш.
Заключение. Графики на рис. 2 наглядно показывают, что у подшипника с медными вкладышами увеличение максимального зазора происходит с существенно меньшей скоростью.
Расчет по данным эксперимента показывает, что предельный максимальный зазор в подшипнике на машине трения может быть, достигнут только после примерно 2 тыс. ч работы подшипника под нагрузкой, или в условиях работы в реальном ДВС через 14000 ч.
Анализ полученных результатов показал, что заменав рядном четырех цилиндровом двигателе алюминиевых вкладышей на медные увеличивает стоимость двигателя всего на 3 %, однако межремонтный период при этом увеличивается почти в десять раз за счет уменьшения затрат на ремонт. Снижаются также эксплуатационные расходы на ремонт, в расчете на 1 час эксплуатации , с 1,8 грн./ч до 1,9 грн./ч или более чем в восемь раз.
Список использованных источников
1. Коровчинский М.В. Теоретические основы работы подшипников
скольжения. – М.: Машиностроение. 1959, - 186 с.
2. Крагельский И.В. Трение и износ. М.: Машиностроение. 1968, - 480 с.
3. Гаркунов Д.Н. Триботехника. М. Машиностроение. 1989, - 327 с.
4. Кугель Р.В. Испытание на надежность машинных элементов. М.:
Машиностроение. 1982. - 181 с.
5. Повышение износостойкости на основе избирательного переноса. Под
редакцией Гаркунова Д.Н. – М.: Машиностроение. 1977, - 121 с.
6. ГОСТ 15467-2002. Управление качеством продукции. Основные понятия, термины и определения. – М.: ИПК изд. Стандартов, 2012. – 26с.
7. Акимов В.М. Основы надежности газотурбинных двигателей: Учебник для студентов машиностроительных специальностей высших учебных заведений. – М.: Машиностроение, 1981. – 207с.
8. Решетов, Д. Н. Надежность машин / Д. Н. Решетов, А. С. Иванов, В. З. Фадеев; под ред. проф. Д. Н. Решетова. - М.: Высшая школа, 2008. - 240 с. editorship of prof. D.N. Reshetova. - M.: Higher School, 2008 .-- 240 p.